The Manufacturing Project That Inspires Faith Oehlerking
Seeing the possibilities of additive manufacturing come to life is all in a day’s work at Beehive.
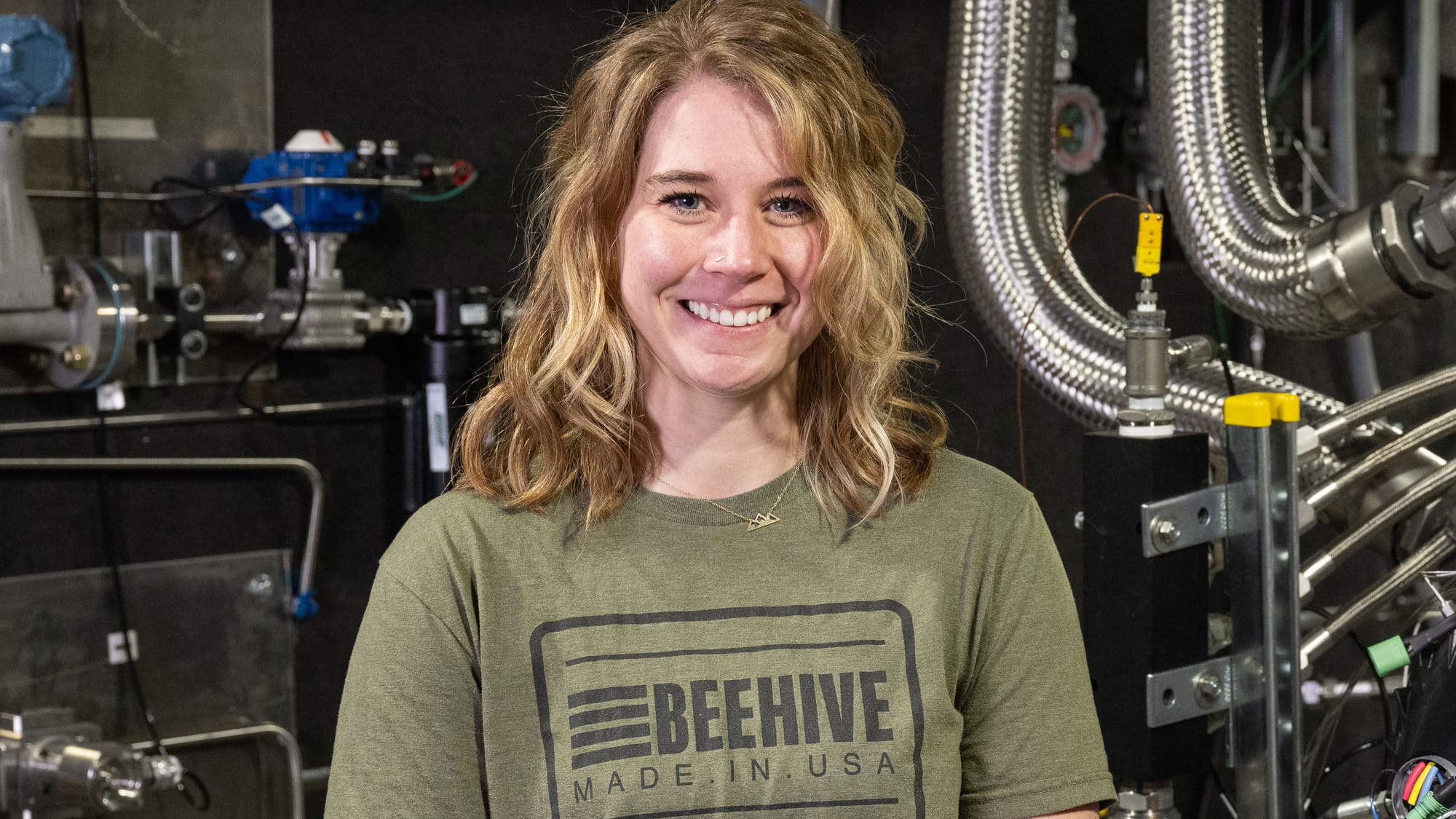
For Faith Oehlerking, Beehive Industries® Senior Manufacturing Programs Leader, the company’s new 500 lb thrust jet engine demonstrator is inspiring, pure and simple.
“Being part of a team that created the concept for the engine, designed and built it within a short time frame, and is now testing its capabilities is a career highlight for me … and we’ve only just started,” explains Oehlerking, who is responsible for ensuring that Beehive’s engine manufacturing program delivers the engine for testing on time and on budget.
500 lb thrust jet engine is only the beginning
Beehive’s first jet engine demonstrator is for unmanned aerial defense applications. It’s a first-of-its-kind 3D-printed jet engine designed and built in the U.S. Oehlerking, who joined Beehive during the startup’s early days, describes the path from concept to test as a thrilling adventure, filled with anticipation and excitement.
“Our Beehive team is not just passionate about what we do, we're dedicated. We’re applying new technologies and developing new processes for manufacturing engines. We’re changing the way an entire industry views engine production. The energy here is infectious.”
Tapping into the advantages of additive
Thanks to additive manufacturing, Beehive was able to deliver the engine for testing at least twice as fast as a traditional engine manufacturer, according to Oehlerking. This significant time saving is attributed to two key advantages.
First, additive manufacturing is efficient. Engineers can move quickly from design to printing parts, testing parts, and refining designs. They can determine if a concept is viable and move ahead rapidly with those learnings. Additive effectively skips the labor- and time-intensive aspect of castings and forgings, which can add months to the process. Teams can print and design at the same time.
Second, additive manufacturing allows for the consolidation of parts. However, consolidation is only one aspect of the advantage. With additive, engineers can design parts that can’t be manufactured with traditional methods and it opens up the field for new design concepts. It also allows the Beehive team to quickly work through issues without losing valuable time.
A team that gets the job done
Oehlerking, who played a vital role in the production of the engine, is always seeking data to move forward and determine best practices.
“I’ve watched the engine go from clean-sheet design to fully assembled and testing,” explains Oehlerking. “We’re constantly improving processes, enabling us to scale production quickly. Additive manufacturing is fast, and we’re unlocking new capabilities each day. Because this is a relatively new technology, there is that sense of excitement. Knowing that we’re capable of more, and then proving it in a short amount of time, offers a tremendous sense of satisfaction. The next day, we turn around and do it again.”
When asked about her experience at Beehive, Oehlerking's response was clear.
“This team is not afraid to get their hands dirty. We are a group that will do whatever it takes to get the job done, and we do it together. The willingness to assist, regardless of the task, is what makes Beehive so fun and collaborative.