Inside Beehive’s Integrated Product Team
Beehive burned down the silos that separate engineers, operations, and manufacturing. That decision transformed how they do business.
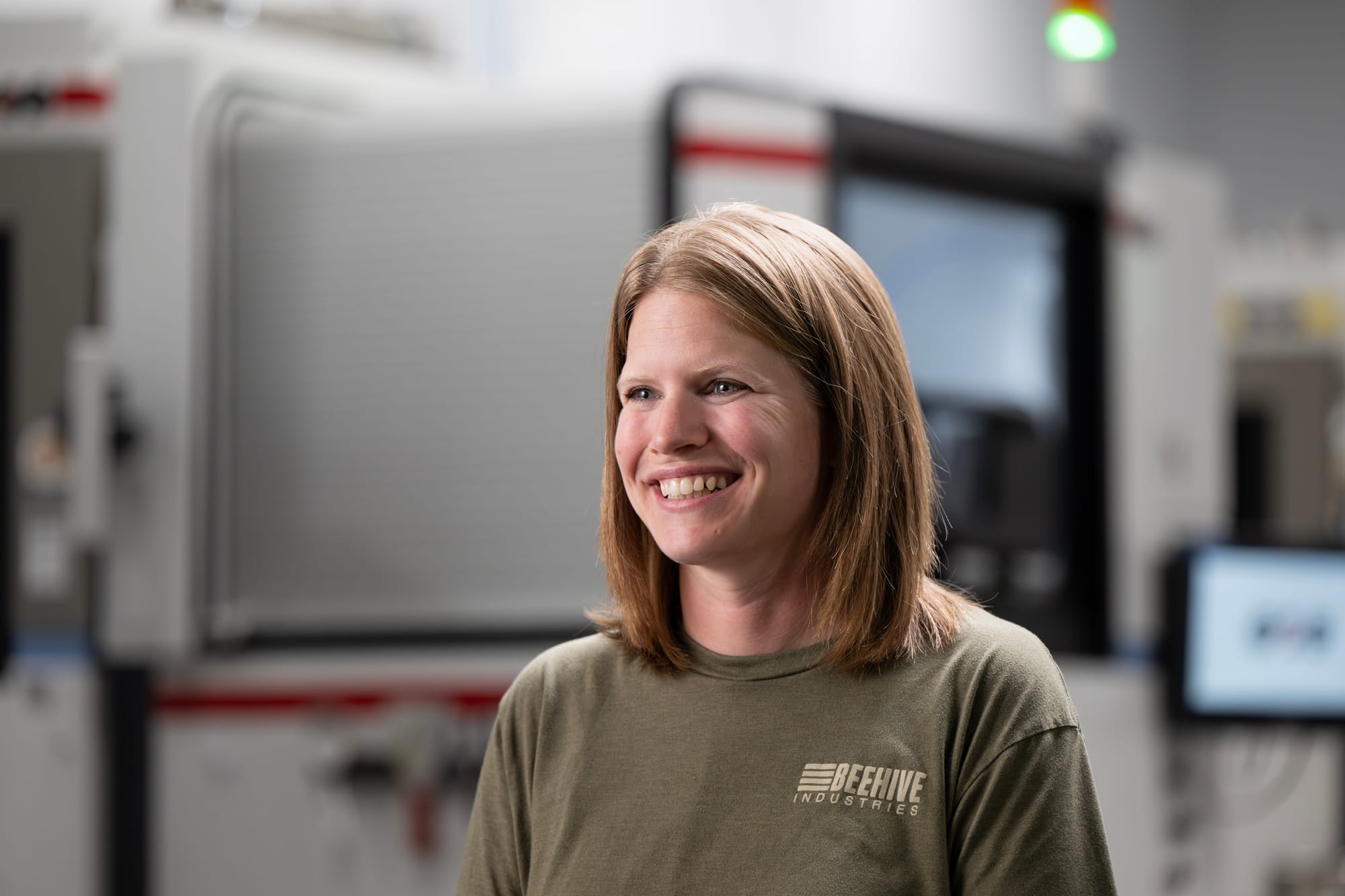
Julie Vaccaro, Beehive Industries’ VP of Manufacturing Programs, is standing in the heart of the company’s Denver facility–a sprawling 60,000-square-foot-hub where some of the most innovative jet engines of a generation are taking shape. Behind her, more than a dozen 3D printers and CNC machines hum quietly while producing new components.
Vaccaro's role is anything but a desk job. Every day, she moves seamlessly between printing labs, engine tests, strategy meetings, and sales calls. She stays part of the action because cross-collaboration is vital to how she, and everyone at Beehive, does business. It’s also what makes her job so fun.
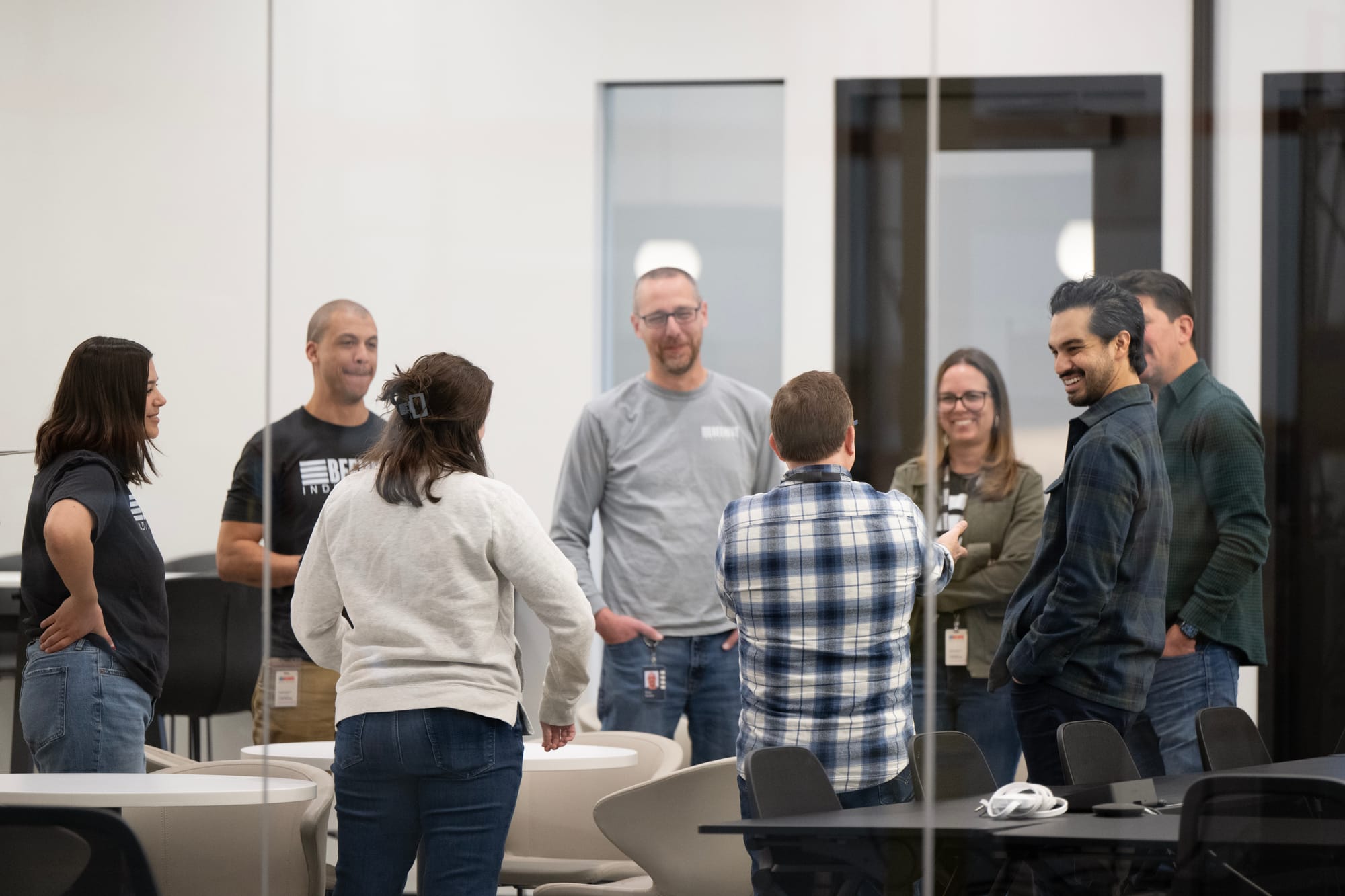
“Part of my role is being the middleman between engineering and manufacturing operations,” says Vaccaro. “I support the full product lifecycle from engineering to final production, ensuring we deliver exactly what our customers need. No two days are the same, and that’s part of what I love. It’s never boring, and it’s very people-focused.”
Vaccaro is a key member of Beehive’s Integrated Product Team (IPT)–a cross-functional group with representatives across the company. Though the idea of IPTs is nothing new–many companies leverage them to speed up processes, streamline decision-making, and improve adaptability–it feels different at Beehive. More than a feature of the business, cross-collaboration lives in the culture. You can see it in everything, from the physical design of the office space to the energy in the breakroom. Everyone here, no matter their background, works together.
“Our integrated product team is so diverse,” shares Vaccaro, “We have chief engineers from large aerospace organizations and scrappy thinkers from young manufacturing shops. Part of the reason we’re able to deliver great products is because of how differently we think and how well we collaborate.”
As Vaccaro shares more about Beehive’s IPT, her team members are demonstrating it in action all around her. Keren Callen, Beehive’s Director of Manufacturing Operations, has made it a point to walk the shop floor and talk to everyone at least once daily.
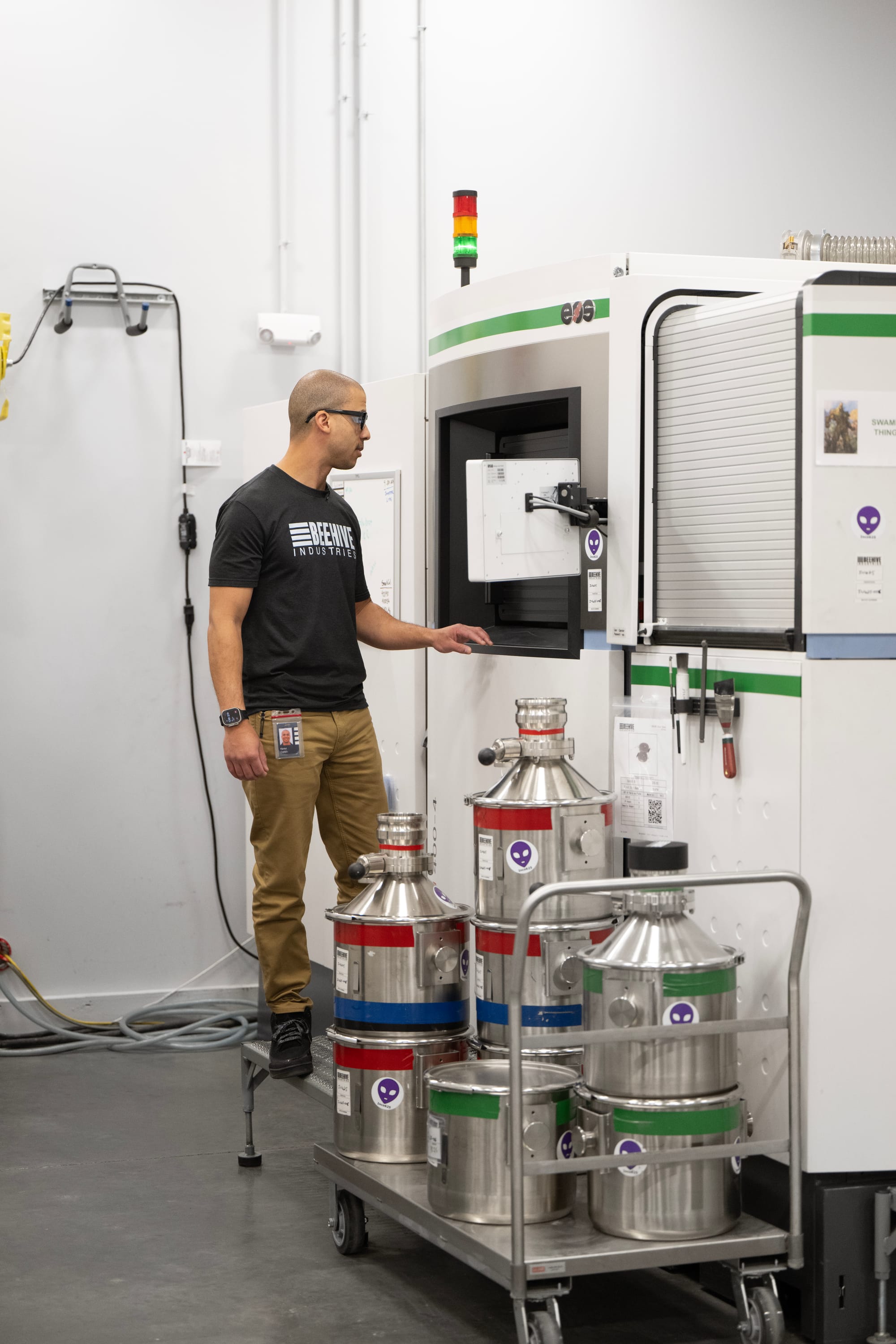
“It would be difficult to work in a silo at Beehive because work is so inherently cross-functional,” says Callen. “I talk to everyone on the shop floor, in the office, and in between, and that helps me get a pulse on what is working well, what isn’t, and if there is anything that needs to be solved or changed.”
Each morning starts with collaboration for Callen and everyone else in Beehive’s IPT. “Design, manufacturing, and quality engineers, as well as technicians and stakeholders, meet every morning to discuss and solve problems that come up in design,” says Callen. “We get to plug real-time feedback from the manufacturing process into design so that we can deliver products that are higher performing and more consistently repeatable.”
Collaborating up the chain of command is just as important as collaborating across departments. “Our integrated product team tracks safety, quality, delivery, cost, goals, and other metrics that are the responsibility of technicians all the way up to the executive suite. It’s about transparency and visibility, and that helps us all stay aligned on the same path,” added Callen.
Jason Chapman, Beehive’s lead test engineer, joins IPT meetings every morning.
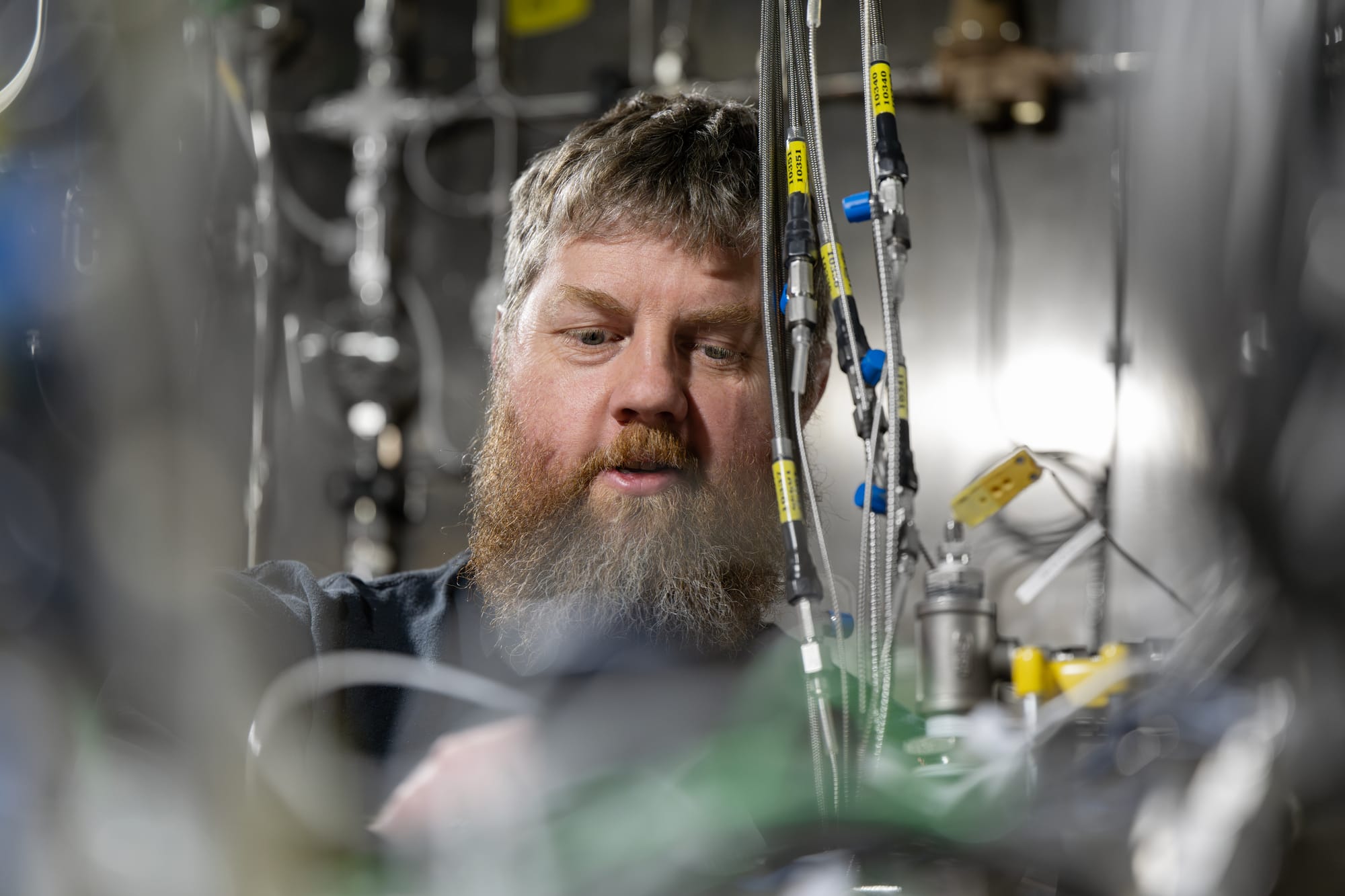
“Part of my job is preparing the engine performance data for each module owner, so they can understand how the product is working and tracking against performance goals,” he says. “We can look at these results together to make sure everyone is meeting requirements or has a plan for how they will.”
It’s not only efficient—it makes for a great experience across both team members and departments. “The best part about working at Beehive is how well we work together,” added Chapman. “We iterate on design and solve problems so quickly because everyone is already fully downloaded and on the same page. I get stumped sometimes. We all do. But I have a full arsenal of people with different backgrounds, coming at these challenges with different considerations and perspectives. We knock out issues fast when we are all in it together.”
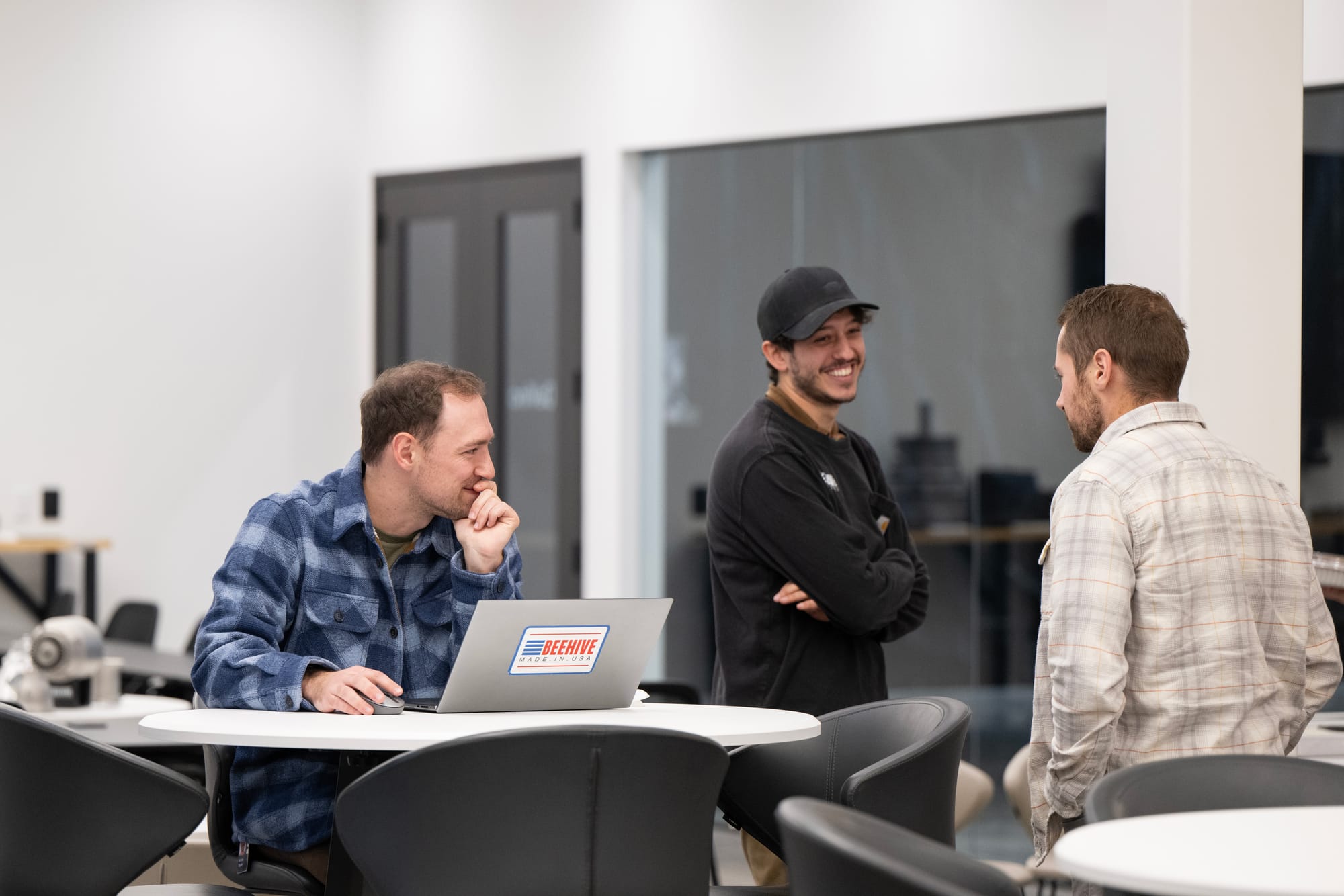
Experiencing the morning IPT meeting firsthand helps to truly understand it all. Across a roundtable of suits, slacks, jeans, and t-shirts, there is debate, discussion, good laughs, and sharp remarks in equal measure. A wildly different group of individuals, all at the top of their respective fields, have committed themselves to a single audacious vision. They’re relentlessly focused, but also open, approachable, and deeply invested in each other’s success.
Beehive has taken on an industry-defining challenge, to power American defense through technology that has never been used at such scale. Through collaboration, real-time problem-solving, and a culture that values innovation, Beehive is proving that complex problems can be solved with the right people and approach. With much to build ahead, one thing is certain—this is the team that can get it done.