How Beehive Builds a new Jet Engine
From a concept to a flight-ready engine, additive manufacturing enables faster, more efficient propulsion development.
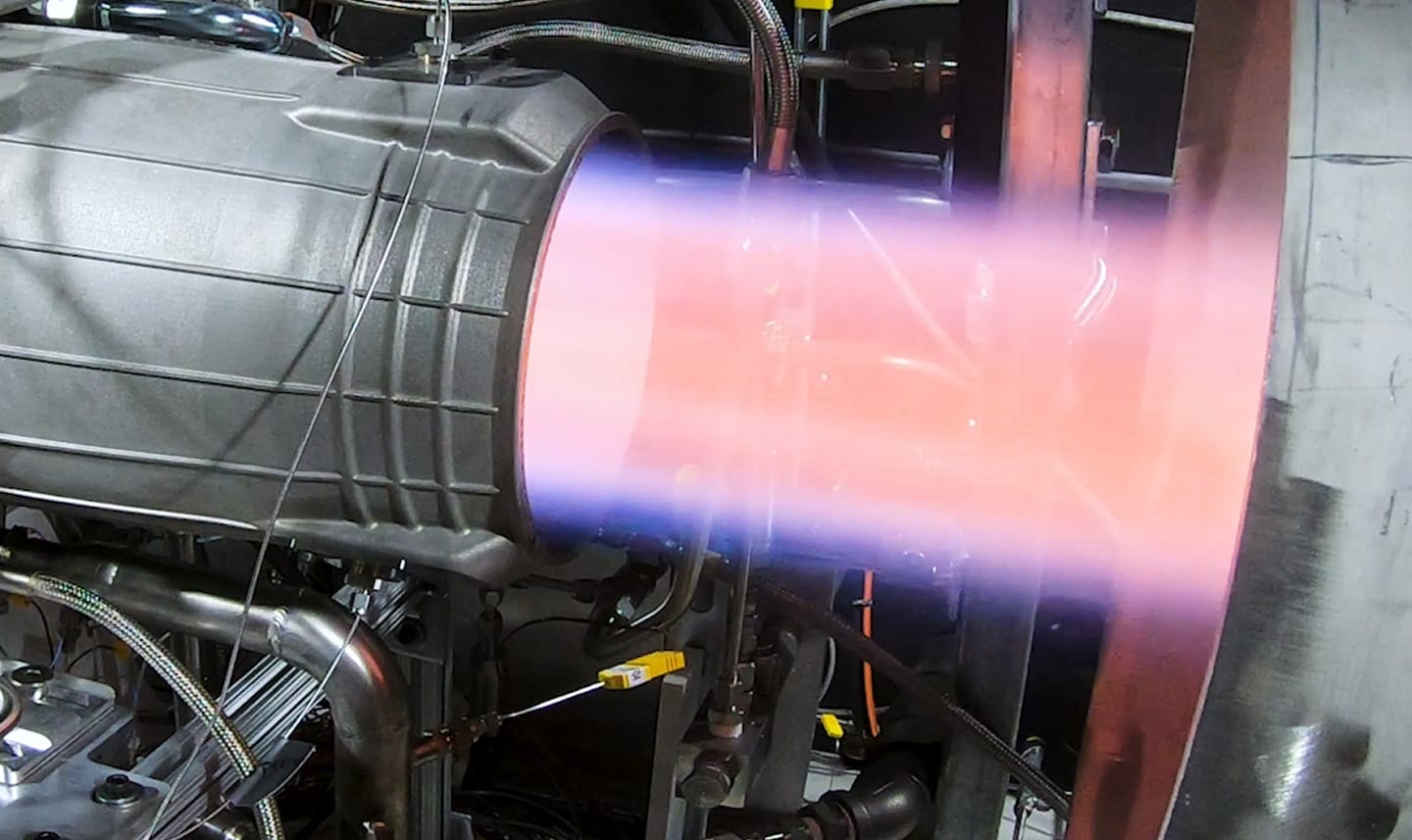
Traditional engine manufacturing relies on carving parts from metal blocks or billets—a subtractive process that’s limited by machine reach and tooling constraints. At Beehive, additive manufacturing allows us to build parts from the ground up, creating unrestricted internal features that support better performance, faster production, and lower cost.
This approach enables lighter, more efficient components optimized for compression, cooling, heat resistance, and strength, specifically designed for unmanned applications.
Here’s how the process works, from initial design to engine validation:
Step 1: Design What Others Can’t Build
Traditional machining comes with limits. If tools can’t reach internal cavities, complex shapes get broken into separate parts, and designs often need to be compromised to fit the constraints of the machine.
Additive manufacturing removes those limits. Engineers can design interdependent features as part of a single component. Every structure and component is built with the end use in mind, not just manufacturability.
Step 2: Print the Impossible
Once the design is locked, the parts go to print without tooling and their inherent delays.
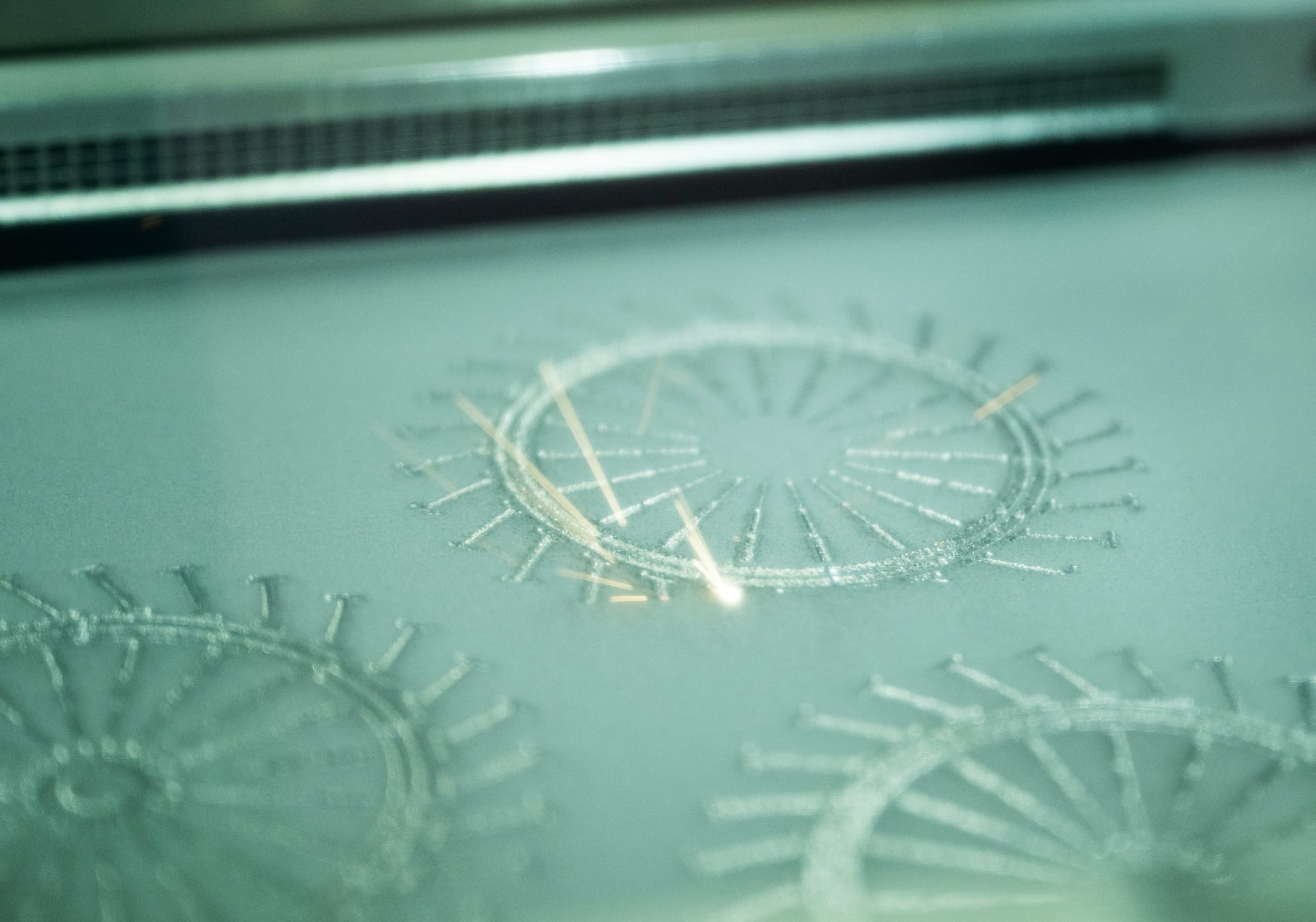
Additive manufacturing builds high-performance modules as a single piece rather than a set of components bolted, welded, or brazed together. Fewer assemblies mean fewer potential failure points, faster assembly, and greater strength precisely where it matters most.
While the printers execute the build, it’s the engineering setup—tuning print parameters—that ensures the result meets design intent.
Step 3: Depowdering
When printing stops, the part is still buried in metal powder. Depowdering removes that loose material and reveals the solid component underneath.
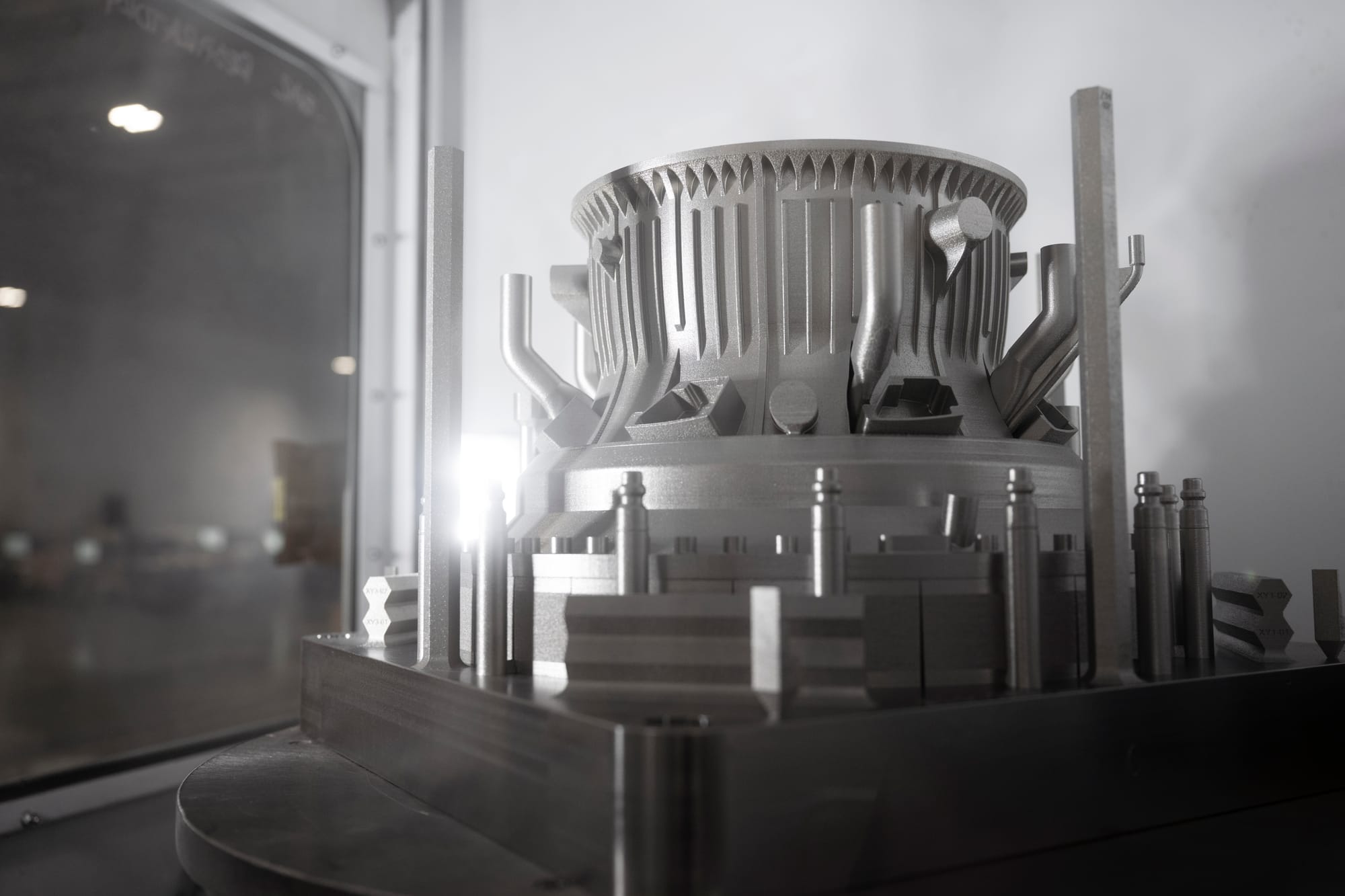
This step prepares the part for inspection, support and build plate removal, heat treatment, and final machining. A clean, powder-free surface is essential for the best possible surface finish and component strength.
Step 4: Heat, Meet Metal
After printing, the part goes through heat treatment to relieve internal stress and strengthen its structure. Heat treatment ensures the material can handle the temperatures, pressure, and vibration of jet propulsion. It’s a crucial step in turning a printed part into a flight-ready one.
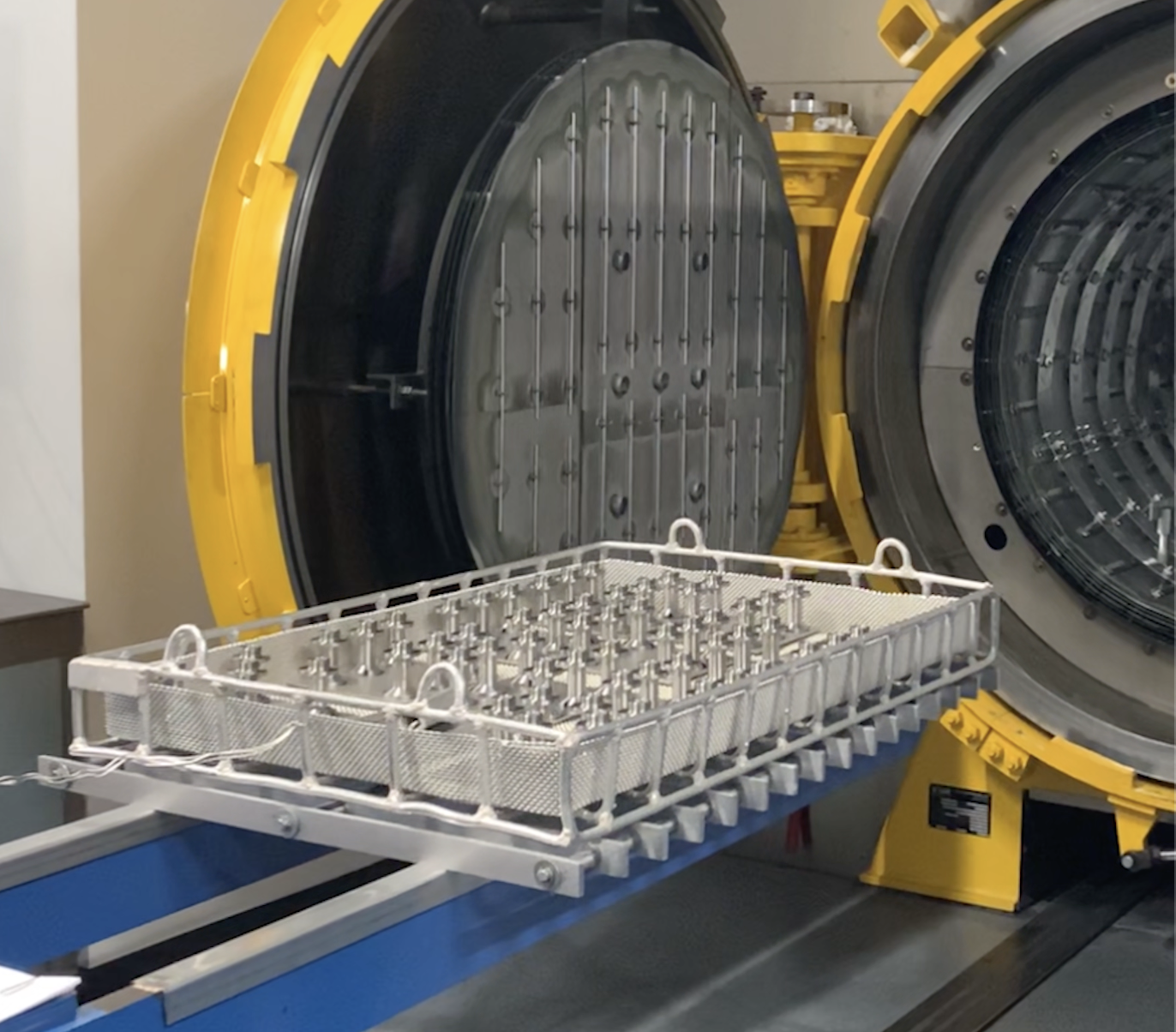
Step 5: Machine for Microns
After heat treatment, some aspects of a part are machined to final spec. This step targets mating surfaces such as module flanges, some rotating interfaces, and other surfaces with the tightest of tolerances. Maintaining these tolerances is essential to an engine's primary function (thrust) and the quality of its performance (fuel efficiency).
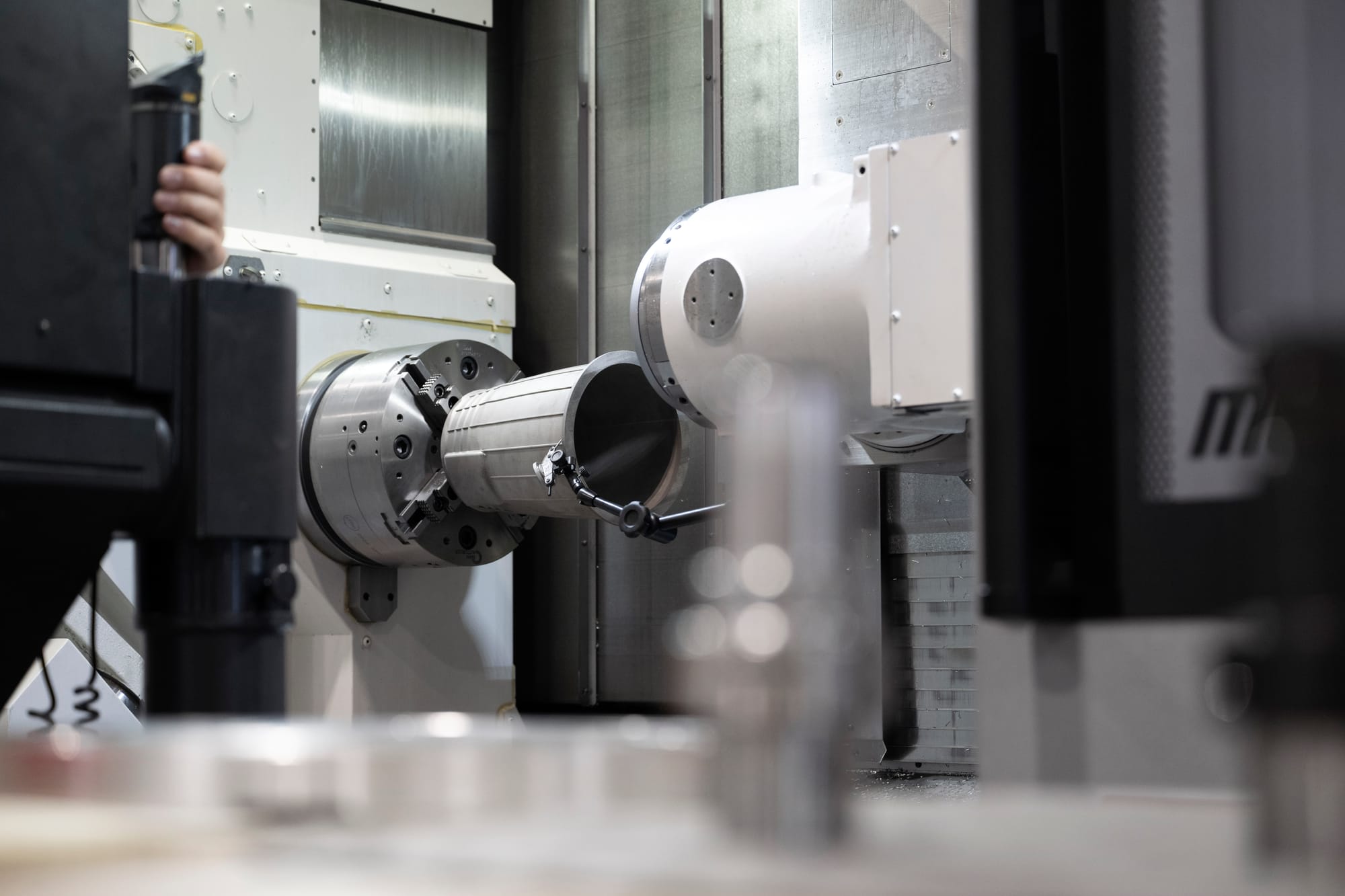
Step 6: Add Insight with Instrumentation
Sensors are added to monitor temperature, pressure, and vibration during testing.
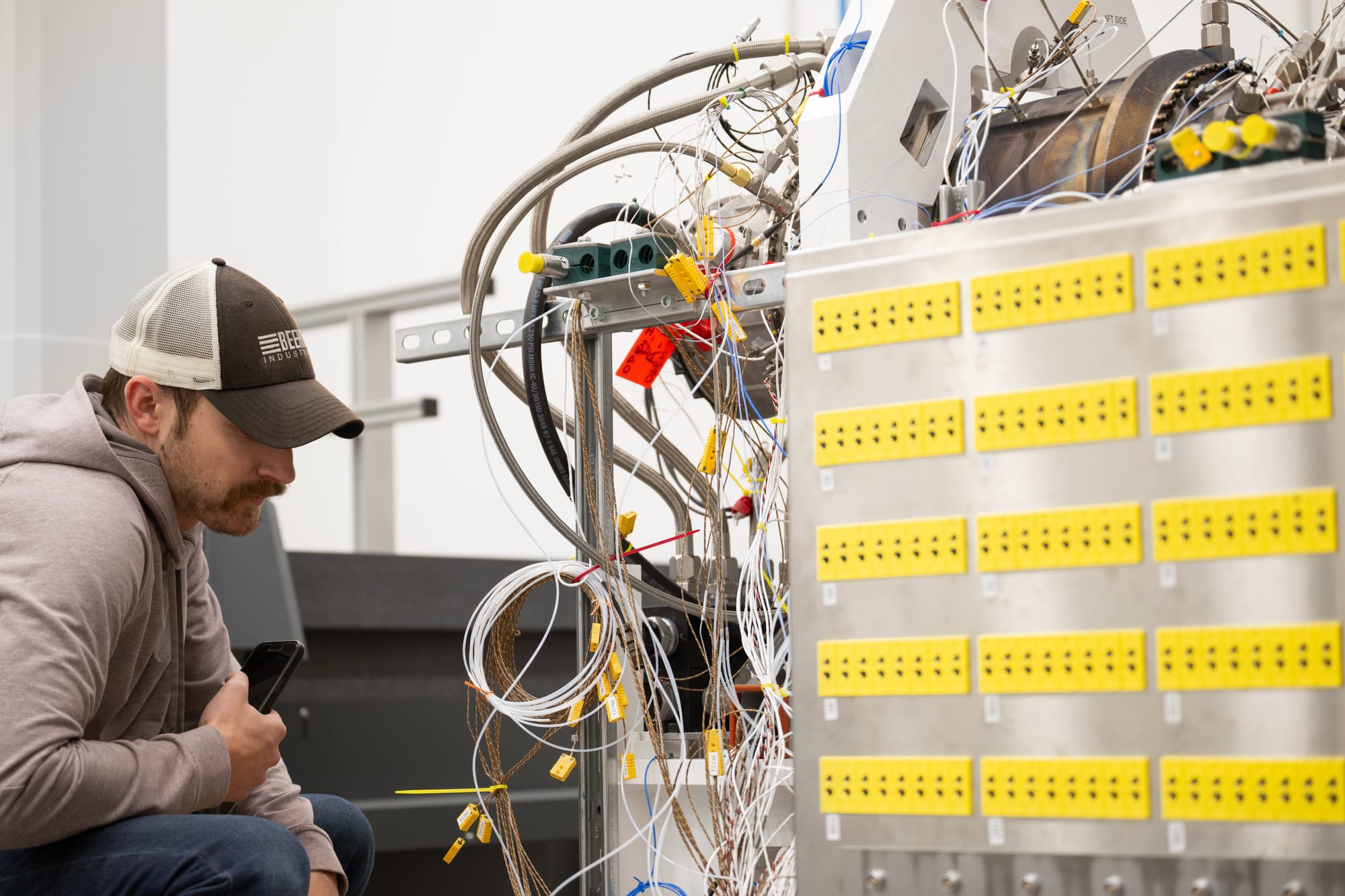
Instrumentation gives engineers real-time feedback on how the engine behaves under stress—turning raw data into insight and insight into improvement. A newly designed engine running through its test phases will have far more of these ports and sensors than a final production engine will.
Step 7: Assembly
Once components are verified, the engine is assembled.
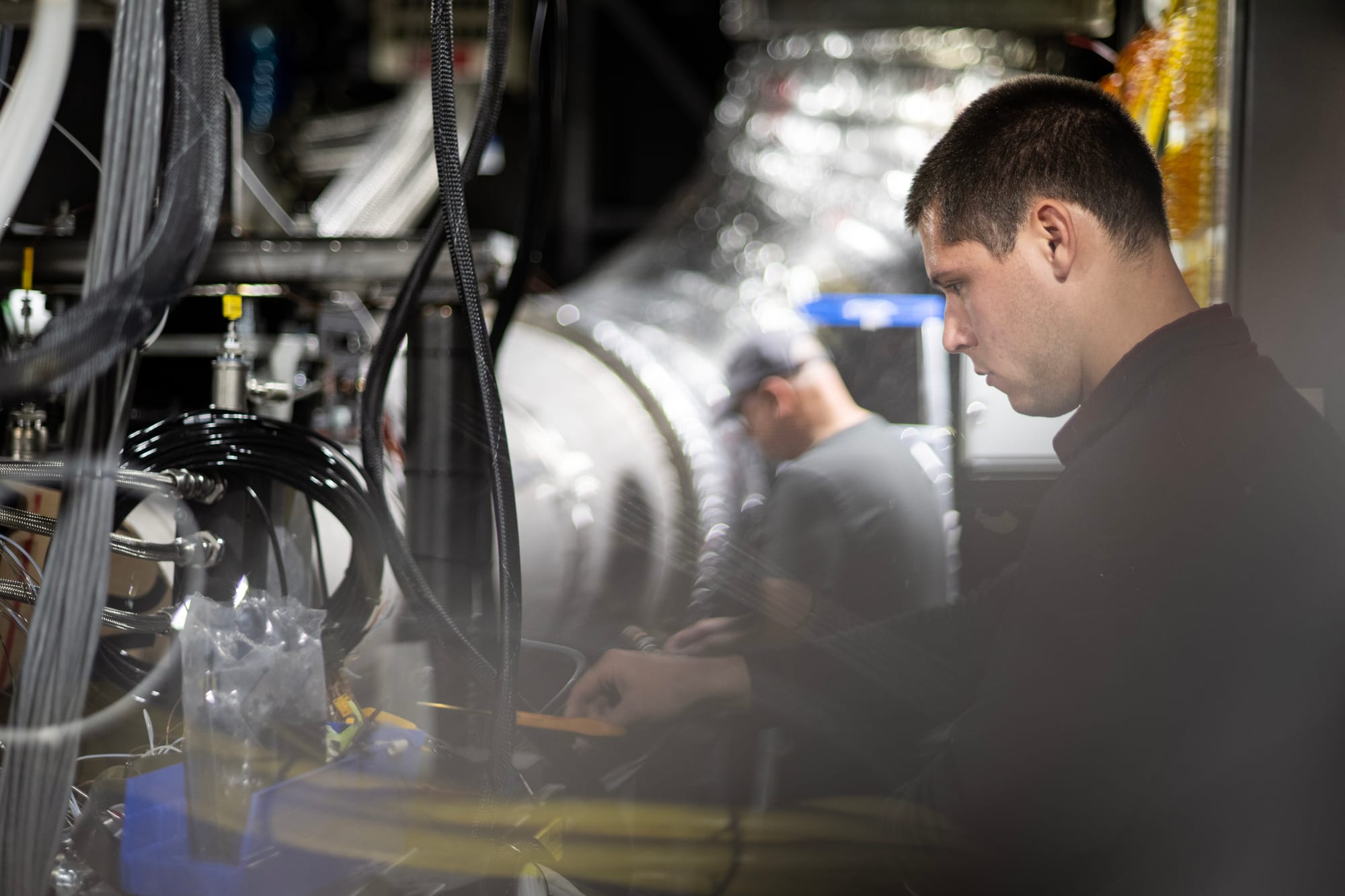
This step represents the integration of static and rotating parts from compression to combustion and finally exhaust. Because engineering and manufacturing teams work together from the start, everything fits and functions as intended. The engine is then installed in the test cell and all the instrumentation is connected to the control room
Step 8: Testing
The finished engine undergoes a full range of testing to simulate real flight conditions—rotation, pressure, vibration, heat, and thrust, and then pushed to the limits to better understand margins. Every data point helps validate performance and confirm the engine is ready for the mission. Testing is where Beehive’s engines earn their wings.
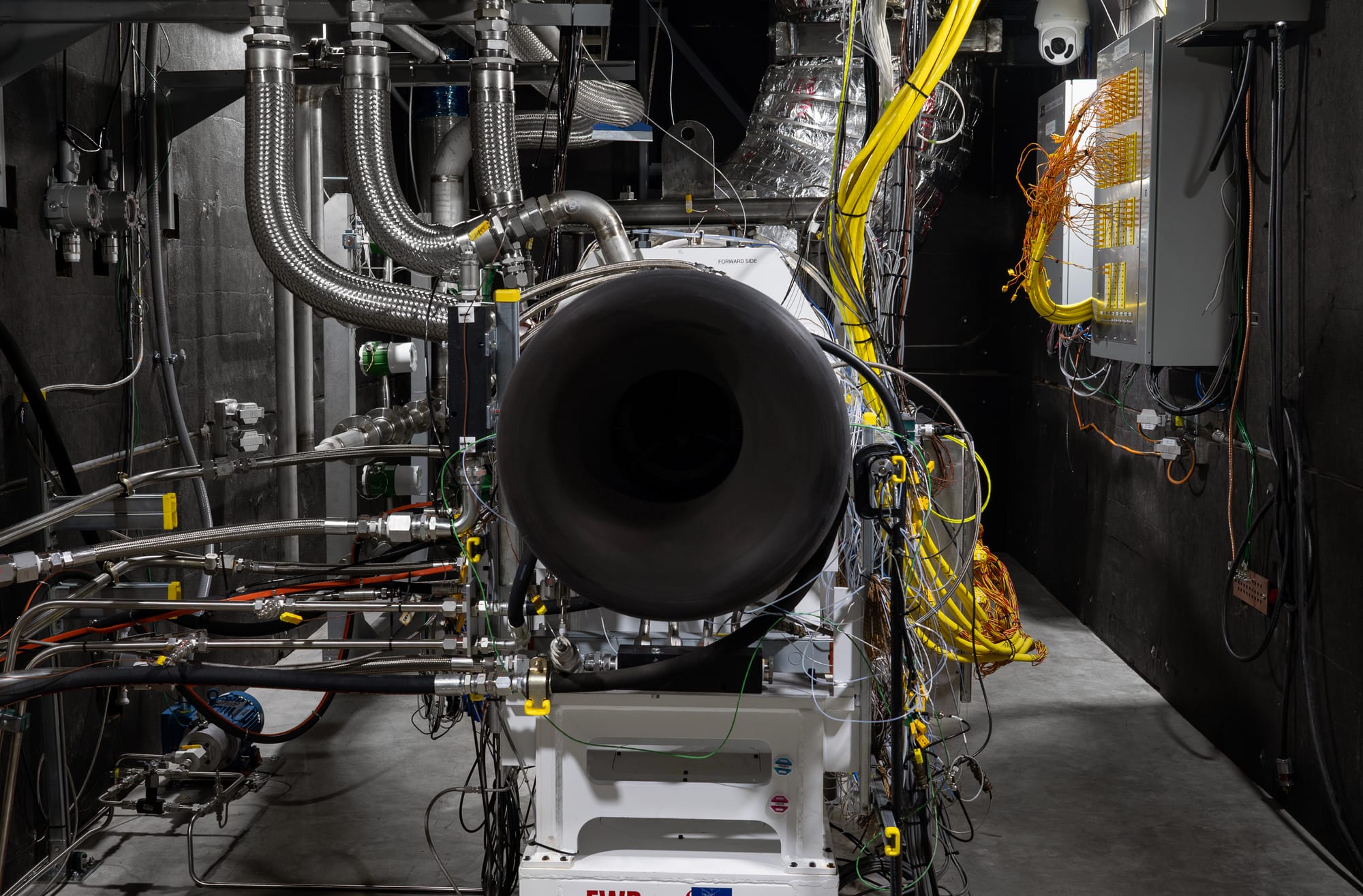
--
This process is about much more than 3D printing. It’s a new approach to designing, building, and delivering jet propulsion. Additive manufacturing allows the flexibility to move faster and build smarter, but the real advantage comes from how it’s put to work, driven by engineering expertise and mission focus.
Beehive builds engines that perform, scale, and meet the demands of modern defense. Want to join the mission? Check out our careers page.